
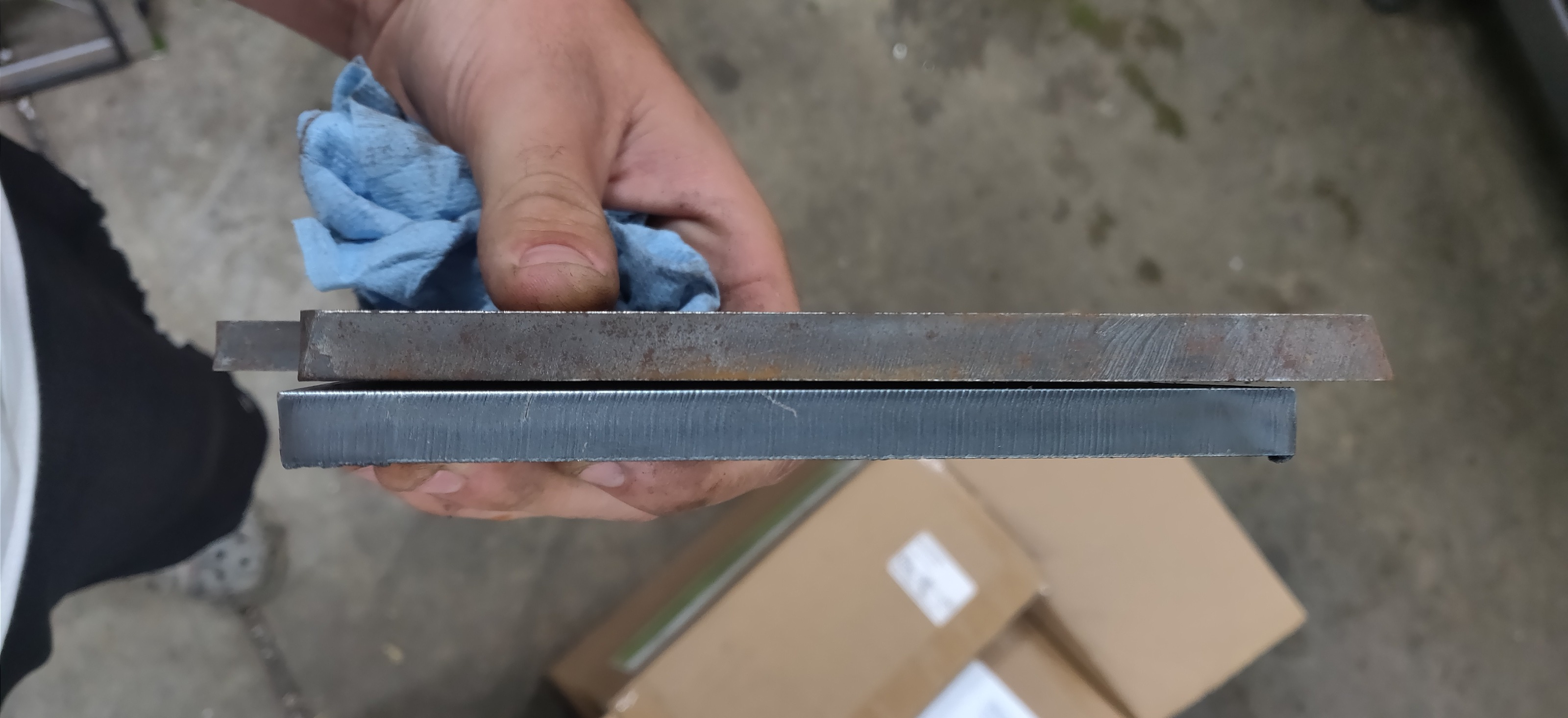
Stepper motors are missing steps (stalling) during programmed motion.īoth rail tubes should be wiped down clean with a dry cloth before and after cutting to prevent the accumulation of dust and debris which can hinder motion.Įxcessive friction between lead screws and lead nuts.
#Sheetcam very slow manual
Please consult the Assembly Manual for the correct procedure for aligning the gantry tube. If all other solutions fail, it is possible that the gantry tube is not level to the surface created by the slat bed.

Gantry tube is not level to slat surface. If the slats are too worn, it may be necessary to purchase a new slat pack. We recommend removing the slag accumulation from the slat bed to re-establish the original bed surface. The table surface is established by the top surface of the slat bed which can become chewed up after repetitive cutting and slag accumulation. If your plate is slightly warped, we recommend using C-clamps to fasten your workpiece down to the slat bed or the machine frame when cutting. Use a straight edge to inspect the flatness of your plate. Most plate is not perfectly flat and it may be possible that your workpiece is warped. Torch height offset is low in some areas of travel and high in others. Please contact Langmuir Systems and submit a support request. If all other solutions fail to produce proper automatic torch firing, it is possible that the electrical relay within the electronics enclosure is not working properly. You may need to use a multimeter to preform a continuity test by manually pulling the plasma torch trigger and testing for continuity between the two wires.Įlectrical relay inside CrossFire TM electronics enclosure is malfunctioning. Inspect that the wires going from the electronics enclosure at the Torch ON/OFF output jack are spliced in correctly to the plasma cutter torch trigger wires. Torch wiring not hooked up correctly to plasma cutter trigger or CNC port.
#Sheetcam very slow full
Inspect that the two wires are plugged in correctly to the Torch ON/OFF output jack on the electronics enclosure and that full continuity is made. Torch wiring not hooked up correctly to Torch ON/OFF port on electronics enclosure If the torch does not fire, it's possible that the plasma cutter or torch has malfunctioned and you will need to contact your plasma cutter manufacturer for resolution.
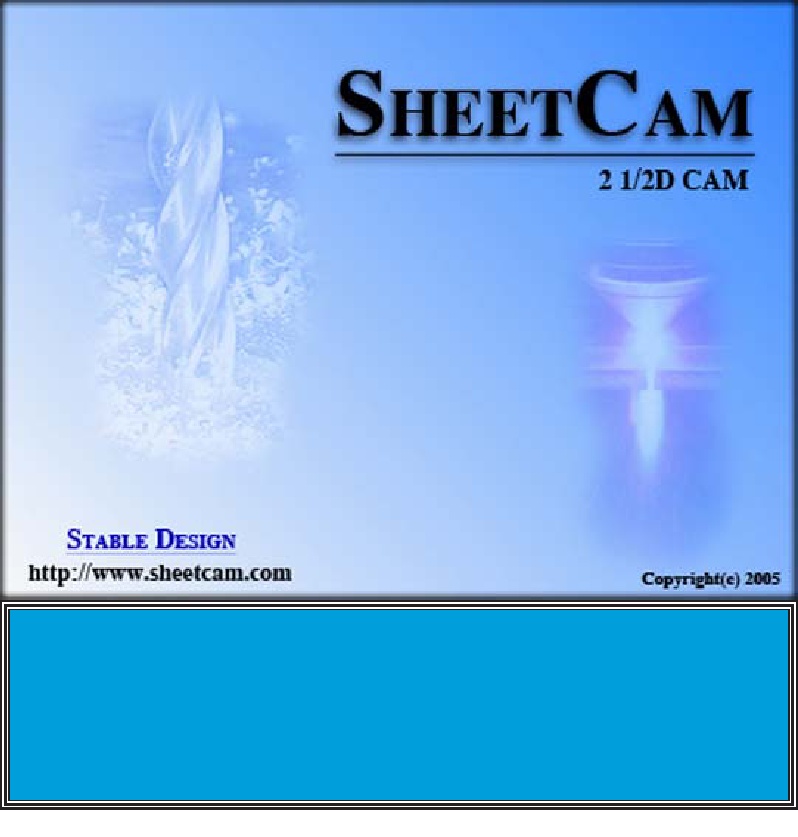
Remove the torch from the torch holder and perform a manual cut off of the machine. Inspect that your plasma cutter is still working properly off of the machine. Also inspect that the plate is not sufficiently rusted or has a coating that will prevent continuity. Inspect that the ground clamp is properly attached. If the pilot arc starts but does not transfer to the work piece, it is possible that the ground clamp is not making continuity to the work piece. Ground clamp not making electrical continuity with workpiece. Please consult your plasma cutter manufacturer for published cutting parameters for your specific model. Lower the cut height in 0.020" increments until continuity is achieved. If the pilot arc starts but does not transfer to the work piece, it is possible that the cut height is too high. Inspect electrode and replace as necessary. Plasma Cutter is not automatically firing or is mis-firing intermittently.
